日期:2017-06-15 / 人气: / 来源:www.biglss.com / 热门标签: 凯时尊龙官网
一提到管理,很多人都觉得十分晦涩难懂,对于制造企业兴起的精益生产管理,那就更觉得难上加难。实际上,精益生产管理十分简单,只需要做好三件事,然后按照pdca的管理模式不断推进、不断改善,就可以达到预期的效果。这三件事就是:规范化管理、标准化管理和简单化管理。推行精益生产管理有哪些好处呢?下面上海博革企业管理咨询有限公司为大家总结出了如下12大好处:
1、消除八大浪费
企业中普遍存在的八大浪费涉及:过量生产、等待时间、运输、库存、过程(工序)、动作、产品缺陷以及管理浪费。
2、降低库存
需指出的是,降低库存只是精益生产的其中一个手段,目的是为了解决问题和降低成本,而且低库存需要高效的流程、稳定可靠的品质来保证。很多企业在实施精益生产时,以为精益生产就是零库存,不先去改造流程、提高品质,就一味要求下面降低库存,结果可想而知,成本不但没降低反而急剧上升,于是就得出结论,精益生产不适合我的行业、我的企业。这种误解是需要极力避免的。
3、关注流程,提高总体效益
改进流程要注意目标是提高总体效益,而不是提高局部的部门的效益,为了企业的总体效益即使牺牲局部的部门的效益也在所不惜。
4、建立无间断流程以快速应变
建立无间断流程,将流程中不增值的无效时间尽可能压缩以缩短整个流程的时间,从而快速应变顾客的需要。
5、全过程的高质量,一次做对
质量是制造出来的,而不是检验出来的。检验只是一种事后补救,不但成本高而且无法保证不出差错。因此,应将品质内建于设计、流程和制造当中去,建立一个不会出错的品质保证系统,一次做对。精益生产要求做到低库存、无间断流程,试想如果哪个环节出了问题,后面的将全部停止,所以精益生产必须以全过程的高质量为基础,否则,精益生产只能是一句空话。
6、基于 顾客需求的拉动生产
jit的本意是:在需要的时候,仅按所需要的数量生产,生产与销售是同步的。也就是说,按照销售的速度来进行生产,这样就可以保持物流的平衡,任何过早或过晚的生产都会造成损失。过去丰田使用“看板”系统来拉动,现在辅以erp或mrp信息系统则更容易达成企业外部的物资拉动。
7、标准化与工作创新
标准化的作用是不言而喻的,但标准化并不是一种限制和束缚,而是将企业中最优秀的做法固定下来,使得不同的人来做都可以做得最好,发挥最大成效和效率。而且,标准化也不是僵化、一成不变的,标准需要不断地创新和改进。
8、精益供应链
在精益企业中,供应商是企业长期运营的宝贵财富,是外部合伙人,他们信息共享,风险与利益共担,一荣俱荣、一损俱损。遗憾的是,很多国内企业在实施精益生产时,与这种精益理念背道而驰,为了达到“零库存”的目标,将库存全部推到了供应商那里,弄得供应商怨声载道:你的库存倒是减少了,而我的库存却急剧增加。精益生产的目标是降低整个供应链的库存。不花力气进行流程改造,只是简单地将库存从一个地方转移到另一个地方,是不解决任何问题的。当你不断挤压盘剥你的供应商时,你还能指望他们愿意提供任何优质的支持和服务吗?到头来受损的还是你自己。
9、满足顾客需要
满足顾客需要就是要持续地提高顾客满意度,为了一点眼前的利益而不惜牺牲顾客的满意度是相当短视的行为。丰田从不把这句话挂在嘴上,总是以实际行动来实践,尽管产品供不应求,丰田在一切准备工作就绪以前,从不盲目扩大规模,保持稳健务实的作风,以赢得顾客的尊敬。丰田的财务数据显示其每年的利润增长率几乎是销售增长率的两倍,而且每年的增长率相当稳定。
10、团队工作
在精益企业中,灵活的团队工作已经变成了一种最常见的组织形式,有时候同一个人同时分属于不同的团队,负责完成不同的任务。最典型的团队工作莫过于丰田的新产品发展计划,该计划由一个庞大的团队负责推动,团队成员来自各个不同的部门,有营销、设计、工程、制造、采购等,他们在同一个团队中协同作战,大大缩短了新产品推出的时间,而且质量更高、成本更低,因为从一开始很多问题就得到了充分的考虑,在问题带来麻烦之前就已经被专业人员所解决。
11、“自我反省”和“现地现物”
精益文化里面有两个突出的特点:“自我反省”和“现地现物”。“自我反省”的目的是要找出自己的错误,不断地自我改进。丰田认为“问题即是机会”-当错误发生时,并不责罚个人,而是采取改正行动,并在企业内广泛传播从每个体验中学到的知识。这与很多国内企业动不动就罚款的做法是完全不同的-绝大部分问题是由于制度流程本身造成的,惩罚个人只会使大家千方百计掩盖问题,对于问题的解决没有任何帮助。
12 、尊重员工,给员工授权
尊重员工就是要尊重其智慧和能力,给他们提供充分发挥聪明才智的舞台,为企业也为自己做得更好。在丰田公司,员工实行自主管理,在组织的职责范围内自行其是,不必担心因工作上的失误而受到惩罚,出错一定有其内在的原因,只要找到原因施以对策,下次就不会出现了。所以说精益的企业雇佣的是“一整个人”,而不只是员工的“一双手”。
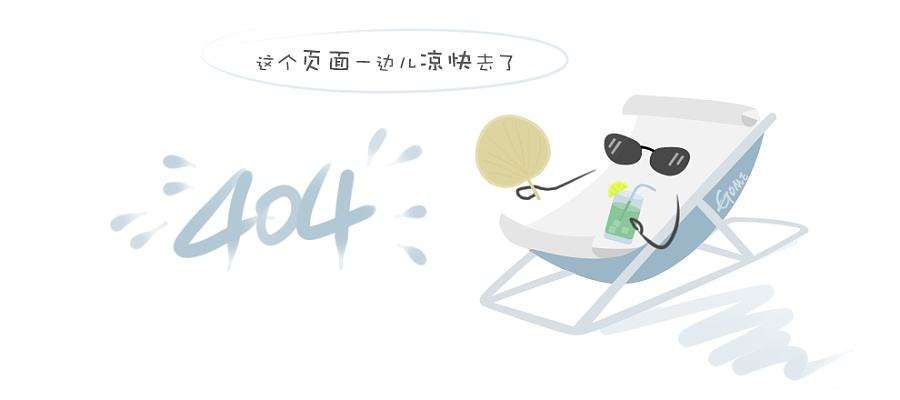
1、消除八大浪费
企业中普遍存在的八大浪费涉及:过量生产、等待时间、运输、库存、过程(工序)、动作、产品缺陷以及管理浪费。
2、降低库存
需指出的是,降低库存只是精益生产的其中一个手段,目的是为了解决问题和降低成本,而且低库存需要高效的流程、稳定可靠的品质来保证。很多企业在实施精益生产时,以为精益生产就是零库存,不先去改造流程、提高品质,就一味要求下面降低库存,结果可想而知,成本不但没降低反而急剧上升,于是就得出结论,精益生产不适合我的行业、我的企业。这种误解是需要极力避免的。
3、关注流程,提高总体效益
改进流程要注意目标是提高总体效益,而不是提高局部的部门的效益,为了企业的总体效益即使牺牲局部的部门的效益也在所不惜。
4、建立无间断流程以快速应变
建立无间断流程,将流程中不增值的无效时间尽可能压缩以缩短整个流程的时间,从而快速应变顾客的需要。
5、全过程的高质量,一次做对
质量是制造出来的,而不是检验出来的。检验只是一种事后补救,不但成本高而且无法保证不出差错。因此,应将品质内建于设计、流程和制造当中去,建立一个不会出错的品质保证系统,一次做对。精益生产要求做到低库存、无间断流程,试想如果哪个环节出了问题,后面的将全部停止,所以精益生产必须以全过程的高质量为基础,否则,精益生产只能是一句空话。
6、基于 顾客需求的拉动生产
jit的本意是:在需要的时候,仅按所需要的数量生产,生产与销售是同步的。也就是说,按照销售的速度来进行生产,这样就可以保持物流的平衡,任何过早或过晚的生产都会造成损失。过去丰田使用“看板”系统来拉动,现在辅以erp或mrp信息系统则更容易达成企业外部的物资拉动。
7、标准化与工作创新
标准化的作用是不言而喻的,但标准化并不是一种限制和束缚,而是将企业中最优秀的做法固定下来,使得不同的人来做都可以做得最好,发挥最大成效和效率。而且,标准化也不是僵化、一成不变的,标准需要不断地创新和改进。
8、精益供应链
在精益企业中,供应商是企业长期运营的宝贵财富,是外部合伙人,他们信息共享,风险与利益共担,一荣俱荣、一损俱损。遗憾的是,很多国内企业在实施精益生产时,与这种精益理念背道而驰,为了达到“零库存”的目标,将库存全部推到了供应商那里,弄得供应商怨声载道:你的库存倒是减少了,而我的库存却急剧增加。精益生产的目标是降低整个供应链的库存。不花力气进行流程改造,只是简单地将库存从一个地方转移到另一个地方,是不解决任何问题的。当你不断挤压盘剥你的供应商时,你还能指望他们愿意提供任何优质的支持和服务吗?到头来受损的还是你自己。
9、满足顾客需要
满足顾客需要就是要持续地提高顾客满意度,为了一点眼前的利益而不惜牺牲顾客的满意度是相当短视的行为。丰田从不把这句话挂在嘴上,总是以实际行动来实践,尽管产品供不应求,丰田在一切准备工作就绪以前,从不盲目扩大规模,保持稳健务实的作风,以赢得顾客的尊敬。丰田的财务数据显示其每年的利润增长率几乎是销售增长率的两倍,而且每年的增长率相当稳定。
10、团队工作
在精益企业中,灵活的团队工作已经变成了一种最常见的组织形式,有时候同一个人同时分属于不同的团队,负责完成不同的任务。最典型的团队工作莫过于丰田的新产品发展计划,该计划由一个庞大的团队负责推动,团队成员来自各个不同的部门,有营销、设计、工程、制造、采购等,他们在同一个团队中协同作战,大大缩短了新产品推出的时间,而且质量更高、成本更低,因为从一开始很多问题就得到了充分的考虑,在问题带来麻烦之前就已经被专业人员所解决。
11、“自我反省”和“现地现物”
精益文化里面有两个突出的特点:“自我反省”和“现地现物”。“自我反省”的目的是要找出自己的错误,不断地自我改进。丰田认为“问题即是机会”-当错误发生时,并不责罚个人,而是采取改正行动,并在企业内广泛传播从每个体验中学到的知识。这与很多国内企业动不动就罚款的做法是完全不同的-绝大部分问题是由于制度流程本身造成的,惩罚个人只会使大家千方百计掩盖问题,对于问题的解决没有任何帮助。
12 、尊重员工,给员工授权
尊重员工就是要尊重其智慧和能力,给他们提供充分发挥聪明才智的舞台,为企业也为自己做得更好。在丰田公司,员工实行自主管理,在组织的职责范围内自行其是,不必担心因工作上的失误而受到惩罚,出错一定有其内在的原因,只要找到原因施以对策,下次就不会出现了。所以说精益的企业雇佣的是“一整个人”,而不只是员工的“一双手”。
作者:博革咨询