日期:2017-06-05 / 人气: / 来源:www.biglss.com / 热门标签: 凯时尊龙官网
精益生产中的七大浪费的第三大浪费是不良品的浪费。主要因素表现为:工序生产无标准确认或有标准确认未对照标准作业,管理不严密、松懈所导致。
产品制造过程中,任何的不良品产生,皆造成材料、机器、人工等的浪费。任何修补都是额外的成本支出。精益的生产方式,能及早发掘不良品,容易确定不良的来源,从而减少不良品的产生。这一条比较好理解,关键是第一次要做正确,但实施起来却很困难。大家不妨仔细想一想,除了产品生产,管理工作中是否也存在类似的浪费情况?
精益生产方式的思想之一就是要用一切办法来消除、减少一切非增值活动,例如检验、搬运和等待等造成的浪费,具体方法就是推行“零返修率”,必须做一个零件合格一个零件,第一次就做好,更重要的是在生产的源头就杜绝不合格零部件、原材料流入生产后道工序,追求零废品率,这是和博革咨询公司“3c现场质量管理法”基本相同的,今后我们应该继续发扬“3c”,并合理地压缩“3c”中“三确认”的时间,进一步完善“3c”。如何消除不良品的浪费呢?博革咨询顾问给出了以下两个方面的解决办法:
一、认真分析与改良不良问题;
对于已经发生的不良品问题,要深入分析,挖掘不良的来源,找到改善的对策,从而保证不再发生类似的不良品问题;
质量问题分析与解决的方法主要是一些qc工具。比如:利用查件表来收集数据、了解质量问题的现状,利用鱼骨图来广泛、深入地分析原因等;(之前我们已经谈过《qc七大手法》,回复“qc”与您分享)
利用pdca循环作为改善的流程进行持续改善质量问题;
二、预防质量问题的出现:
“第一次就要把事情做正确”。大幅度提升首次合格率,推行“零返修率”,必须做一个零件合格一个零件,第一次就把事情做好。
要做到“不制造不良品”“不流出不良品”“不接收不良品”。
尽可能在生产的源头就杜绝不合格零部件、原材料流入生产后道工序,最求零废品率、零缺陷。
比如:采用清晰的标识、颜色管理、不同容器等防止误用、混料等差错事故的发生。此外,通过合理的定置管理,将合格品、待检、返修、报废、待处理等物料分区域放置,也避免将不良品流入到生产过程中。
不良品的产生是本就不该发生的问题,但如果我们不能及时解决,只会让不良品的问题不断的发散,未来的问题会越积越多;所以一旦发生不良,我们要立即解决,并且要确保未来的产品不会有同样的不良发生,一次解决所有的问题;
不良品不会消失,但我们要用我们200%的热情与200%的耐心去不断的解决产生这些不良品的问题,让我们用所学到的知识去解决产生这些不良的问题。
产品制造过程中,任何的不良品产生,皆造成材料、机器、人工等的浪费。任何修补都是额外的成本支出。精益的生产方式,能及早发掘不良品,容易确定不良的来源,从而减少不良品的产生。这一条比较好理解,关键是第一次要做正确,但实施起来却很困难。大家不妨仔细想一想,除了产品生产,管理工作中是否也存在类似的浪费情况?
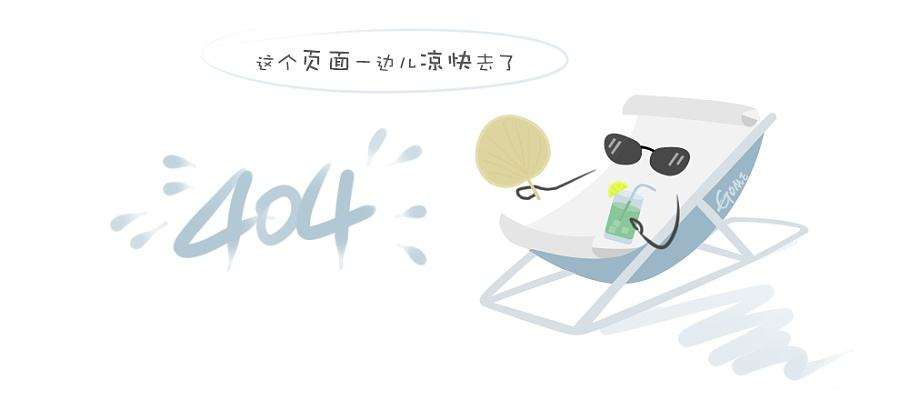
一、认真分析与改良不良问题;
对于已经发生的不良品问题,要深入分析,挖掘不良的来源,找到改善的对策,从而保证不再发生类似的不良品问题;
质量问题分析与解决的方法主要是一些qc工具。比如:利用查件表来收集数据、了解质量问题的现状,利用鱼骨图来广泛、深入地分析原因等;(之前我们已经谈过《qc七大手法》,回复“qc”与您分享)
利用pdca循环作为改善的流程进行持续改善质量问题;
二、预防质量问题的出现:
“第一次就要把事情做正确”。大幅度提升首次合格率,推行“零返修率”,必须做一个零件合格一个零件,第一次就把事情做好。
要做到“不制造不良品”“不流出不良品”“不接收不良品”。
尽可能在生产的源头就杜绝不合格零部件、原材料流入生产后道工序,最求零废品率、零缺陷。
比如:采用清晰的标识、颜色管理、不同容器等防止误用、混料等差错事故的发生。此外,通过合理的定置管理,将合格品、待检、返修、报废、待处理等物料分区域放置,也避免将不良品流入到生产过程中。
不良品的产生是本就不该发生的问题,但如果我们不能及时解决,只会让不良品的问题不断的发散,未来的问题会越积越多;所以一旦发生不良,我们要立即解决,并且要确保未来的产品不会有同样的不良发生,一次解决所有的问题;
不良品不会消失,但我们要用我们200%的热情与200%的耐心去不断的解决产生这些不良品的问题,让我们用所学到的知识去解决产生这些不良的问题。
作者:博革咨询